Desarrollo y fabricación de medidor de CO₂ en espacios cerrados para determinar la calidad del aire
Actualmente, la medición de la concentración de CO₂ en espacios cerrados se ha puesto en boga por la pandemia de COVID-19, debido a que, si las personas están enfermas, exhalan CO₂ junto con una carga viral. Por tanto, para espacios cerrados donde conviven grupos de personas, se puede inferir de forma indirecta que una baja concentración de CO₂ implicará una carga viral baja. Ante esto, los dispositivos para medir CO₂ ayudan a tomar decisiones relativas a la ventilación en áreas de trabajo, hogar, lugares de esparcimiento o áreas cerradas donde se concentre un grupo de personas.
Con el empleo de medidores de CO₂, tomando como referencia la tabla de la fig. 1, podemos determinar si un espacio necesita de ventilación o bien si es apto para desarrollar actividades. Es claro que por debajo de las 750 ppm la calidad del aire será buena, entonces, se debe buscar que no sobrepase las 1000 ppm, sobre todo para evitar aletargamiento en las personas que ocupen un espacio.
Ante el eminente regreso a actividades presenciales en la Universidad Nacional Autónoma de México (UNAM), con el fin de que se contara con un equipo que permitiera a las autoridades, profesores, investigadores y trabajadores en general, determinar si el espacio donde realizan sus actividades cuenta con una buena ventilación, se propuso a las autoridades de la UNAM, con el apoyo de la Dirección del Instituto de Ingeniería, un proyecto con el objetivo de diseñar y fabricar equipos de medición de CO₂ para espacios cerrados. El dispositivo debe ser portátil, compacto, fácil de usar, con una alarma audible y visual para avisar de altas concentraciones de CO₂ previamente fijadas por el usuario. Además, debe ser operado por baterías recargables y operar con un solo botón.
Con lo anterior en mente y con el objetivo de hacer un buen diseño, se seleccionó en primera instancia el sensor. A nivel comercial hay gran variedad de sensores de CO₂ en los que su confiabilidad depende mucho del método de medición y esté en buena medida fijo su costo. Se determinó que, el sensor, además de ser confiable debía tener un costo razonable.
Los sensores de bajo costo, en general, son de tipo electrolítico, pero tienen un alto consumo de energía y no son exclusivamente sensibles al CO₂, su lectura es afectada por otros gases, mientras que los de mayor costo son los de tipo infrarrojo, estos en general son sólo sensibles al CO₂.
Se contactó a la empresa china Zhengzhou Winsen Electronics Technology Company debido a que es fabricante de estos sensores y comercializa diferentes modelos con diferentes principios de medición, además de que ésta fue la única compañía que nos ofrecía la posibilidad de una venta directa minimizando los costos de intermediación.
Se obtuvieron muestras de los sensores MG812 y MH–Z19X (figuras 2a y b) de Winsen; el primero de tipo electrolítico y el segundo de tipo infrarrojo. Las pruebas realizadas determinaron que el MG812 es susceptible a la temperatura, a vapores de alcoholes y solventes de pintura, por lo mismo, a pesar de su bajo costo, no se seleccionó.
Por otra parte, el MH-Z19X que se basa en una medición infrarroja no dispersiva y que es específico para utilizarse en espacios cerrados, no es susceptible al vapor de agua, es poco sensible a los vapores de alcoholes y solventes, cumple con la confiabilidad deseada y tiene un precio que se ajustaba al presupuesto previsto para el sensor.
Debido a que se deseaba que el dispositivo tuviese una pantalla gráfica OLED y pudiera volverse un adquisidor, se seleccionó un microcontrolador de 32 bits que permitirá manejar una pantalla gráfica OLED, incluso a futuro, mostrar gráficas de la concentración contra el tiempo.
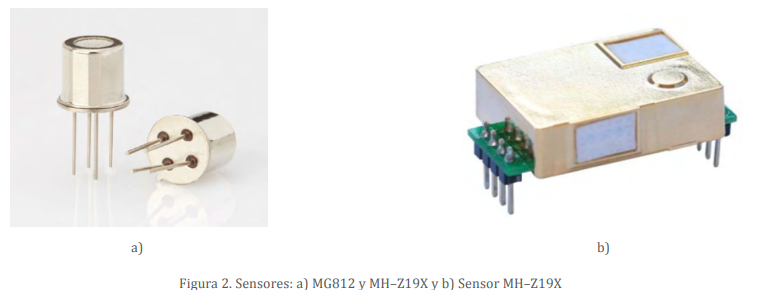
Con el objetivo de realizar un desarrollo en un periodo corto, se diseñó un circuito impreso base, sobre el cual desarrollaron y probaron cuatro rutinas básicas: manejo de la pantalla, adquisición de datos, manejo de transductor y manejo de energía, logrando en un periodo de tres meses el primer prototipo.
Cabe notar que el diseño mecánico del chasis se inició a la vez que la electrónica, por lo cual, el primer circuito sólo cumplía parámetros electrónicos, pero no mecánicos.
En cuanto al firmware se realizaron dos versiones, una de sólo monitoreo, la otra de monitoreo y captura. La versión de sólo monitoreo permite que el usuario fije el valor límite, para que cuando éste se sobrepase se emita una alarma óptica y acústica; esta última puede ser apagada por el usuario con el objetivo de evitar molestias si se está monitoreando, por ejemplo, un salón de clases.
La segunda versión permite, además de fijar el límite de alarma, fijar los parámetros de muestreo necesarios a fin de que cuando se conecte a una computadora por el puerto USB, puedan ser bajados los datos adquiridos por este medio y así, hacer estudios de espacios de alto uso, como salones, auditorios y laboratorios. A los equipos distribuidos dentro de la UNAM se les cargó un firmware de sólo monitoreo, mientras que a los distribuidos dentro del Instituto de Ingeniería se les cargó el modo de captura y registro.
La LADIMMA fue encargada de realizar el diseño mecánico del chasis, con el objetivo de contar con una carcasa de diseño único, que fuera ergonómica, de uso fácil e intuitivo, cuidando que el material usado fuera adecuado a la aplicación, para lo cual, se tuvo que definir de forma previa todos los elementos mecánicos para que se acoplaran mecánicamente con el chasis y que éste tuviese todos los elementos de fijación y apoyo necesarios, evitando el uso de tornillería adicional.
El diseño de la carcasa se inició una vez que se determinó el modelo definitivo de la pantalla OLED, el número de botones, el número y tipo de indicadores luminosos, el modelo de batería y el modelo del sensor. Se realizaron cuatro etapas de diseño que fueron: diseño conceptual, evaluación del diseño final, diseño del molde y fabricación del molde.
De los modelos conceptuales y finales se obtuvieron modelos impresos en 3D con el objetivo de observar el resultado final para realizar verificaciones y correcciones necesarias antes de que se diseñara el molde final del chasis y pasar a la fabricación; la figura 3 muestra el diseño final del chasis.
Debido a que no se cuenta con la capacidad de ensamble de tarjetas electrónicas en alto volumen, se recurrió a la empresa Marpatel, quien se encargó, usando maquinaria Pick & Place, del ensamble de todos los componentes electrónicos incluyendo pantalla y sensor, además de cargarle el firmware, que también permite una verificación rápida del ensamble. Lo anterior dio como ventaja una alta confiabilidad al ensamble, disminución de los errores por intercambio de componentes, además, dado que Mapartel, es experta en este rubro, cuenta con todos los procedimientos y buenas prácticas para el manejo de semiconductores llevando a prácticamente cero el desperdicio de componentes. Esta acción disminuyó de manera muy importante el tiempo de ensamble y pruebas finales, quedando solamente la verificación eléctrica después de la instalación de la batería y el montaje dentro de la carcasa.
Así pues, el proceso de verificación previo a la entrega de los equipos a la Dirección General de Proveeduría de la UNAM, consistió de dos tareas, la primera fue la verificación de conexión y carga por medio del puerto USB, mientras que la segunda fue la verificación de la lectura.
Para realizar la primera tarea, se conectó cada uno de los equipos a un puerto de una PC por medio de un adaptador que medía la tensión y corriente suministrada por el puerto. Con esto se verificaba que el equipo fuera reconocido y enumerado. La verificación del controlador de carga de la batería se hizo cuidando que la corriente suministrada estuviese dentro de los parámetros establecidos.
La segunda tarea, que fue verificar que la lectura fuera correcta, se logró al saturar un área, usando hielo seco (CO2 sólido), para después ventilarlo de manera paulatina y controlada, verificando que las lecturas fueran coherentes con respecto a un patrón. Los dispositivos con lecturas fuera del estándar se separaban para ser llevados a un ambiente de 400 ppm para ser calibrados mediante un procedimiento establecido por el fabricante, el cual se programó en el firmware, para lo cual, se desarrollaron algunas rutinas en LabView.
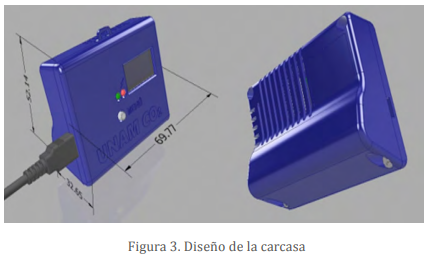
Junto con el equipo se entregó un cable y cargador para que el Kit estuviera completo. También, se tiene abierto un correo de atención para que si el usuario tiene algún problema con el equipo lo pueda reportar.
Como conclusión, el desarrollo del diseño y la producción del equipo de medición de CO2 fueron satisfactorios, se desarrollaron en un periodo corto, prácticamente en el tiempo pactado, no obstante los retrasos debidos a los problemas de abasto de materiales por la pandemia y al hecho de tener que cambiar algunos componentes, como por ejemplo el modelo del micro controlador.
El diseño demostró ser lo suficientemente robusto para permitir cambios sin la necesidad de modificar el PCB o la carcasa.
Debido a la aceptación que tuvo el equipo por los usuarios de las diferentes dependencias de la UNAM, se solicitó la fabricación de quinientos equipos adicionales.
Se agradece a la Secretaría Administrativa del Instituto de Ingeniería, así como a Proveeduría de la UNAM, por su apoyo en el proceso de compras y a las empresas que colaboraron en la producción de los equipos.